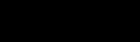 |
   |
Variously called Engine Turning, Jeweling, Damascening, Krayling, Guilloche (if enameled), Snailing, a decorative pattern of overlapping swirls on metal that are variously thought to reduce glare, or hold oil on surfaces, but in truth are just beautiful to look at because they catch the light and reflect moving wedges as the item or the viewer moves. Likely to be found on rifle bolts and vintage automobile dashes. If overdone, will be denigrated as gaudy, but eye-candy in small amounts.

These instructions are for end brushes used in a drill press, not for cratex rods or abrasive pads like scotchbrite. Brushes have a distinct advantage on the sharp edges of metal projects; abrasive pads will shred. Brushes also have an advantage on curved surfaces, remaining in contact with your project more than, say, a flat disc of sandpaper or the fabled dowel in a drill press. Nothing uglier than incomplete contact resulting in a partial swirl pattern.
1. Make sure the surface is clean, polished and shiny before you begin. Jeweling a rusty, corroded, pock-marked, or uneven surface doesnt work, leaves distinctive eyes and magnifies any area not throughly scratched by the swirl pattern. In general, dont rely on jeweling to hide much; its ability to cover irregularities on the surface of your project are overrated. Go to the extra work of sanding or polishing the piece bright before beginning. Random patterns work best (like sanding with a random orbital sander), or straight (like stoning or sanding in one direction) but dont use a file or coarse sanding paper that can leave large scratches, which will show through your swirl pattern and ruin it.
2. Use the right end brush. From my experience, you want a wire end brush made of carbon steel or stainless steel (aluminum projects require stainless steel brushes, as carbon will embed and rust), although these brushes can be somewhat aggressive for brass or copper projects. Get straight bristles if you can (but most are crimped). I havent had good luck with brass brushes or nylon brushes, which tend to polish the surface or leave noticeable eyes in the center, but they may be appropriate for some softer materials. Choose a brush with fine bristles; you can find them with bristles of .006. Coarse bristles (such as .013) can gall the center, or the eye, of the swirl and actually dig ugly potholes into your project. Most end brushes are meant to remove material quickly, which means that most end brushes are ineligible for engine turning. The right brush makes all the difference in the quality of outcome. Run the brush at a moderately high speed on the drill press.
3. Use a slurry of cutting oil and abrasive (120 grit silicon carbide powder is common) on your project. The slurry of abrasive and oil is necessary, even for nylon brushes that have abrasives built in. Dont try to get along without the slurry or a dull polished pattern will likely result. What makes the pattern beautiful is the sharply etched but shallow swirls that catch the light. The oil helps keep the brush bristles sharp.
4. Bridle or bind your brush with shrink tubing (or O-rings or tape or whatever) before starting; without this you get an inconsistent spread of the brush. I wrap crimped wire brushes with a little masking tape to get the bristles under control, and then go over that with shrink tubing which pulls the bristles in tight. For example, an unbridled 3/16 brush gave me circles from 7.8-8.6mm in diameter. Bridled with 3 layers of shrink tube, it gave 8.0-8.1mm diameter circles. More sophisticated options exist, such as the engine turning brush holder sold by Brownells.
5. Chrome plated items you can jewel them, but the scratches may get down to the copper level beneath the chrome, giving the product a pink look. You may want to experiement with a softer brush (such as nylon or brass) and a fine abrasive if you want to try it, but test your setup on something chrome you dont care about, and wait a couple days for the exposed copper to darken. My best-looking projects have been solid metal (steel, iron, aluminum, brass) with no coating or plating.
6. Test your step-and-repeat distance. A compound slide works best. I dont have one (yet), so I use either my 4 cross slide vise, or a small stationary vise attached to a block of wood that I scoot on top of a laminated paper grid pattern (this requires careful alignment before each swirl and is thus slow, but effectivesee the plane below that was jeweled in this primitive fashion). Attractive jeweling overlaps the previous swirl such that the eye from the previous swirl is seen, but not so much that there is a gap of unscratched space between swirls. If your brush is giving you trouble with eyes, you can shorten the distance between swirls so that the edge of a subsequent swirl goes through the eye of the previous. That gives you a more crowded look to the jeweling, and is slower, but it is a fix for a brush that isnt cutting in the center.
7. Beware of flash rusting on your iron or steel project. You may need to coat the freshly jeweled surface immediately after cleaning with a protective finish, such as clear spray lacquer. You might try using alcohol rather than water to remove the slurry on pieces that will flash rust, and then spray or brush on a coat of clear protective finish right away.
Brush Impressions:
--- 3/16 Brushes
Brownells 080558003, 3/16 (4.8mm) Engine Turning Brush. One of the few non-crimped brushes available. Gives approx 7mm swirl diameter after bridling and break-in, which works well on a 5mm grid (the result is well proportioned and shows the eye of the previous). Bristle is .005 (.13 mm) wire steel. Its on the small side, but the best brush so far. Gives wonderful results. Superior performance.
--- 1/4 Brushes
MSC 00079830, 1/4 Stainless Steel Miniature Crimped End Brush. Bristle is .005 (.11 mm) stainless steel wire. Gives 8mm (?) swirl. Unknown performance.
--- 5/16 Brushes
MSC 00079848, 5/16 Stainless Steel Miniature Crimped End Brush. Bristle is .005 (.11 mm) stainless steel wire. Gives 8mm (?) swirl. Unknown performance.
MSC 05013610, 5/16 Miniature Crimpled End Brush. This looks like a very good brush. Mildly crimped but not bushy, with a thick midsection. Unknown performance.
--- 1/2 Brushes
MSC 00126409, 1/2 Brass Bridled End Brush, gives 16mm diameter swirl. Bristle is thin brass .005 (.11 mm) wire. Too soft for steel, leaves a polishing effect without scratches. Poor performance.
MSC 00126912, 1/2 Nylon Abrasive 320 Grit End Brush. Gives 16.5 swirl diameter. Leaves a distinct eye in the middle of the pattern. This brush leaves a softer pattern (even with abrasive added), a less distinct circumference, but a distinctive eye. The brush itself does not appear to scratch. Mediocre performance.
MSC 00462648, aka Weiler EBA-20. 1/2 Crimped Wire End Brush with .006 wire. Very bushy with a large flare, possibly difficult to bridle. Unknown performance.
MSC 00357012, aka Anderson 06901. 1/2 Crimped Wire End Brush with .006 wire, not quite as bushy as the otherwise similar Weiler. Unknown performance.
--- 5/8 Brushes
MSC 88934773, 5/8 Nuline brass coated steel end brush, gives a 19.5 swirl diameter and is way too aggressive in the center. Heavy .32 mm bristle (.0129 wire diameter). It makes deep pits for eyes and will ruin the surface. Failing performance.
--- 3/4 Brushes
MSC 03019924, 3/4 Nylon 120 Grit End Brush. X performance.
Bristle Conversions:
.0129 = .32 mm (heavy/coarse; too coarse)
.0100 = .25 mm
.0060 = .15 mm
.0050 = .13 mm (Brownells brush)
Resources:
http://www.cs.ucr.edu/~eamonn/et/et.htm
http://www272.pair.com/stevewag/jb/jb.html
http://www.midwayusa.com/rewriteaproduct/802575
http://www1.mscdirect.com/cgi/nnsrhm
http://www.brownells.com/aspx/NS/store/ProductDetail.aspx?p=608&title=ENGINE+TURNING+BRUSHES
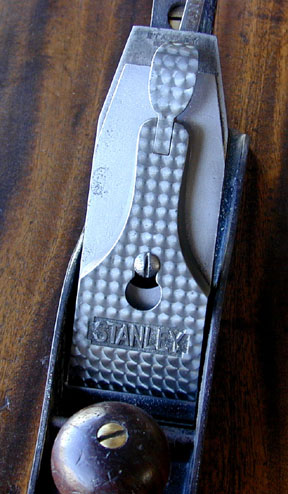
Copyright © 2004 K Rhoads
www.workingpsychology.com
|